Hierarchical Composite Design
The overarching aim of NextCOMP is to improve the absolute performance of composites in compression, both to address practical limitations of the current materials, and as a demonstration of the value of quantitative hierarchical materials design found in nature.
Our research will develop and embed structure at every length scale from the molecules of the matrix, to the lay-up of final components, using new constituents and new architectures, designed within a new analytical framework. The vision of the Programme Grant is realised through six flexible and highly interlinked research activities;
-
Slide-pack
Please feel free to share this document and if you have any queries please do not hesitate to contact the Team.
-
Mechanistic Modelling
Computational modelling is an essential tool for advancing state-of-the-art composites, establishing both fundamental mechanisms and optimising specific parameters. In NextCOMP, new analytical and finite element models will be combined, to establish the most important opportunities to improve composite compression performance. The results will be validated by detailed in-situ mechanical studies and used to identify, understand and prioritise particular experimental strategies.
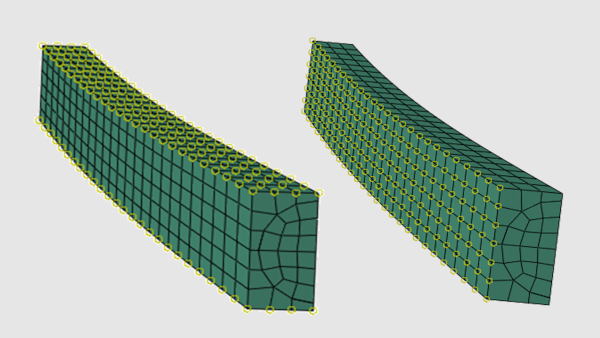
M Patni ©
Models with fine mesh elements are used to predict the interactions between fibres, resin (matrix), and their interface under compressive loads.
Resin Systems
In composites, attention often focusses on the high strength and stiffness of the primary reinforcing fibres, rather than the resin matrix that holds them together. However, the matrix typically accounts for around half the total composite volume and is especially important in determining the performance in compression. The challenge is to improve the stress and stiffness of the resin, particularly as it shears between the fibres, without reducing the toughness of the composite (the ability to resist cracks). NextCOMP will explore a range of strategies including;
- newly developed commercial resins, as yet unused in fibre composites,
- entirely new resin systems with internal multiscale architecture,
- the addition of pre-synthesised nanoscale reinforcements to introduce hierarchy.
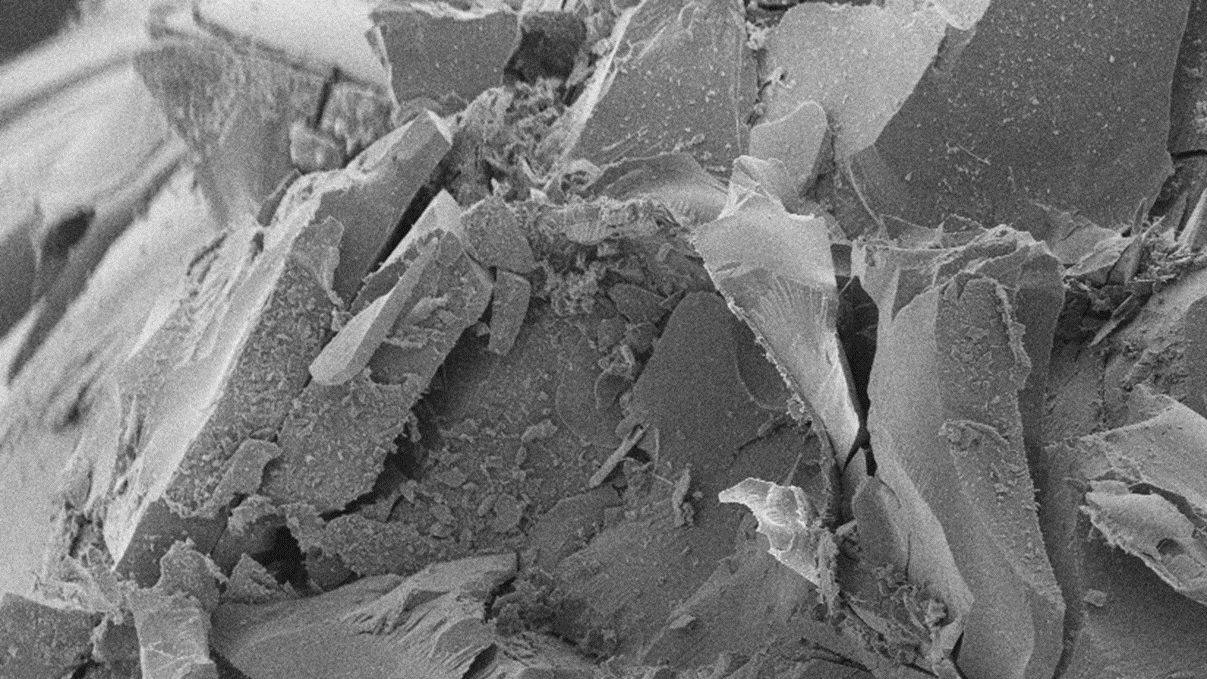
DB Anthony ©
Epoxy resins are used predominantly in fibre reinforced composite materials, the fracture surface above shows a resin rich region after a brittle catastrophic failure.
Fibre Platforms
Current state-of-the-art composites use high performance fibres to carry load in particular directions; the most common examples exploit carbon or glass fibres. On the whole, fibre materials have been developed for tensile loads which are well suited to their geometry. The full intrinsic performance of fibres in compression is generally not exploited in composites, due to other failure mechanisms, for example those associated with the resin matrix. NextCOMP will explore whether different types of fibres or fibre surface treatments can access a greater proportion of the underlying compression performance, using a range of strategies including;
- more complex or non-circular cross-section fibre shapes,
- nanomaterial inclusion/surface modifications,
- hybridisation of different fibre materials.
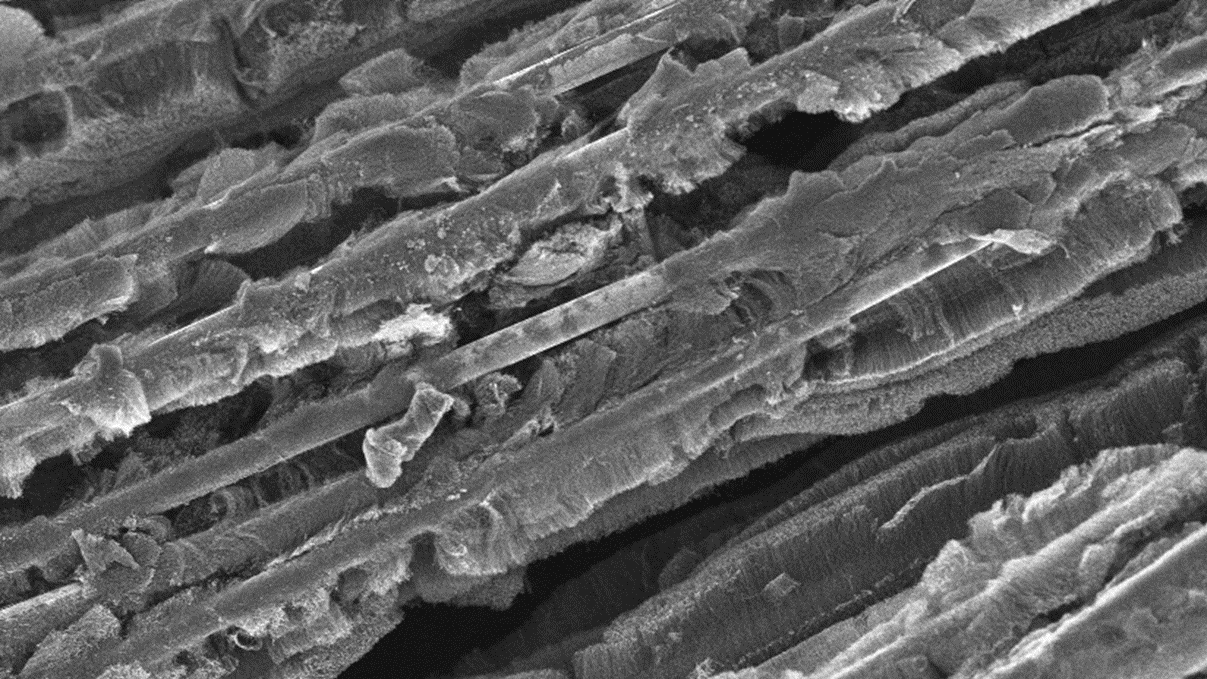
HG De Luca ©
Fibres can be modified with carbon nanotubes, which appear like hairs on the fibres under an electron microscope. This method of modification alters the critical interface/interphase between the fibre and the surrounding resin in fibre reinforced composites.
Ply Level Systems
Many polymer-matrix composites are assembled in layers (or plies) of aligned fibres. Delamination of these layers often contributes to composite failure, especially in compression. NextCOMP will develop innovative ply level designs for composite materials and their structures, in compression, aiming to delay the events leading to failure, or control how and where damage develops. NextCOMP will take inspiration from a number of biological motifs, but quantitatively redesigned to exploit existing start-of-the-art materials, and those developed during the programme. The potential outcomes of ply level designs will include;
- maximising longitudinal compressive strain (overall deformation) and the energy dissipated during failure,
- preventing certain failure modes occurring by design,
- arresting or redirecting an unstable, rapidly growing (i.e. 1km/sec), compression crack.
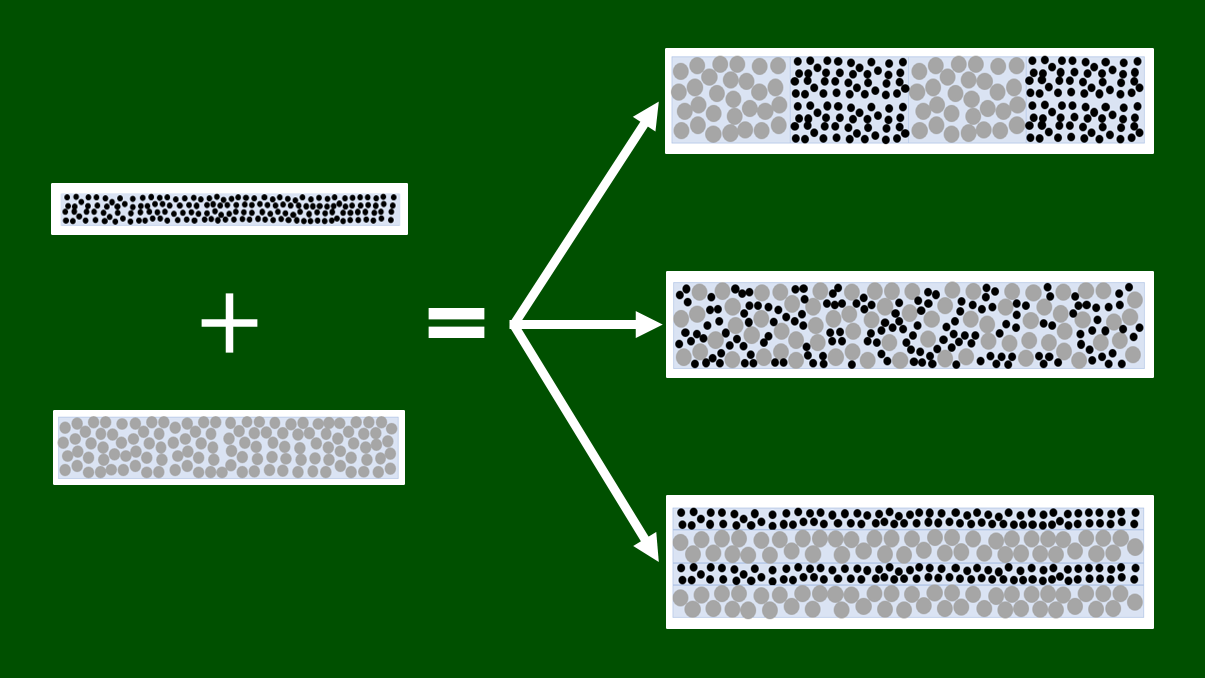
T Garulli ©
A combination of complimentary reinforcing fibres, mixed at the ply level, can drastically effect the composites overall performance. Altering the volume of each component, the way in which they are combined, and the choice of materials can alter the way the composite fails.
Bundle Systems
Many natural hierarchical systems, including wood and bone, exploit fibrous motifs arranged in bundles of bundles. Mimicking natural hierarchical structures is a significant challenge, but one clear design principle is that reinforcement over many length scales is effective. This part of the programme will explore how to use different combinations of bundles fibres to maximise compression performance, again using quantitative computational methods to design target architectures. These bundled systems allow a greater control of alignment, which is known to be very important in compression, whilst allowing spatial modulation of fibre and matrix properties. These designs will span the length scales between the micro- to millimetre range, but can be built up to form larger structures.
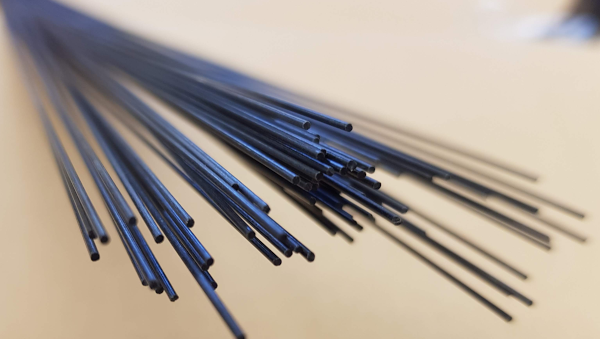
LR Pickard ©
A close up of pultruded carbon fibre reinforced rods, with each rod containing approximately 1000 carbon fibre filaments. The fibres in these rods are all aligned in the same direction along the rod-axis. These rods can be made in-house or bought commercially and are the starting material used to investigate bundle systems.
In-situ Mechanistic Studies
Computational models are only as good as the information which is supplied to them. The data required go beyond those values commonly reported for matrix, fibres, and their combinations, either in the scientific literature or provided by manufacturers. It is, therefore, essential to measure the relevant material parameters, experimentally. In fact, surprisingly, many of the key parameters are not generally measured at all. In such cases, new experimental methods will need to be designed to evaluate these material properties in practical ways, which still represent the conditions of use.
As the project develops new materials and mechanisms to improve compression performance, in-situ observations of the damage that develops under load will help to confirm, understand, and improve implementation.
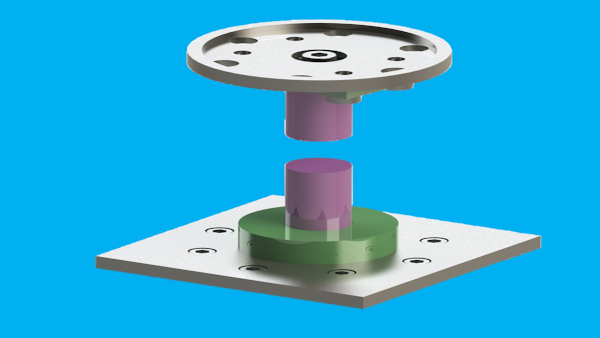
GQ Quino ©
Virtual testing allows new jigs and holders, and methods to be evaluated before manufacture. Once designed they can be made in-house to our own specifications and use to accurately determine material properties.